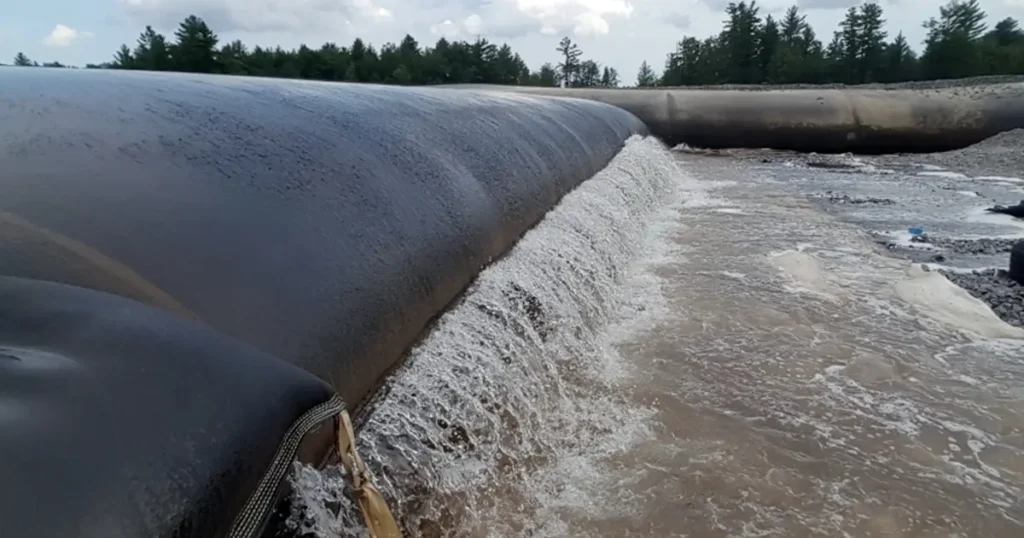
ARTICLE
The advantages of low-energy, high-performance Geotube® dewatering for biosolids management
Spinning, squeezing, solar drying, there are many ways to dewater sludge from treatment plants and produce stabilized biosolids that are ready for land application or disposal. Selecting the best approach often considers several factors, including the speed at which dewatering must be completed, the space that’s available at the treatment plant to accommodate the process, and capital and operating costs.
Simple solutions such as solar drying may seem less costly initially, but the process is laborious and time-consuming and may drive up staff costs. Mechanical processes may work more quickly, but often incorporate complex, energy-intensive mechanical equipment that is costly to buy, maintain and operate.
Geotube® Geotextile dewatering of wastewater sludge provides simple, low-energy operation, efficient dewatering with little operator attention, and a customizable footprint to fit the plant configuration.
Single-step process for solids collection, consolidation and dewatering
The Bishop Solids Management Solution is used by municipal and industrial treatment plants throughout Canada to capture, dewater and consolidate solids in a single step. The system incorporates Geotube geotextile containers and a unique Venturi Emulsion Polymer Activation System (VEPAS™) to do the bulk of the work. Dewatering is achieved largely by gravity, which helps reduce capital cost, simplifies operation and makes the system very energy efficient. Electricity is required only for the sludge feed pump and the VEPAS.
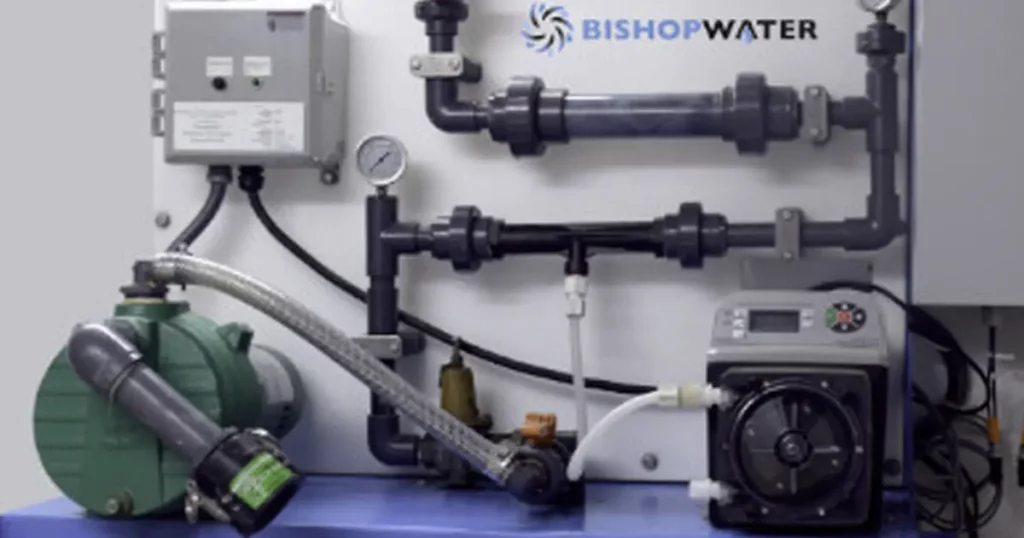
The compact VEPAS automatically activates and injects polymer in a single step to enhance dewatering and retain contaminants.
Geotube containers are made from a high-strength, tightly woven polypropylene fabric that provides both containment and filtration. Solids can be pumped directly from sludge storage tanks, lagoons or digesters to the Geotube. Along the way, the VEPAS activates and adds polymer on the fly, directly into the sludge feed line. This innovative system can operate automatically and eliminates many of the components in mechanical polymer systems, such as mixers and tanks, which take so much time to maintain and clean.
The specially selected polymer performs several functions in the process. It accelerates the dewatering process, enabling filtrate to flow almost immediately through the pores of the Geotube container and preventing clogging. The polymer also helps retain BOD, TSS and many other organic and inorganic contaminants in the dewatered solids.
Depending on the application and discharge regulations, the filtrate could also meet permit limits for release into a receiving body or non-potable reuse. At a municipal treatment plant, the filtrate would typically be sent back to the headworks for treatment prior to discharge.
Filling a Geotube container usually occurs in batches, so it may take several pumping sessions over a period of weeks or months before the container is full. After each session, the container is allowed to dewater, which reduces the volume and creates space for additional sludge to be added. This process can occur year round, even in cold climates. Where temperatures fall below freezing, a greenhouse can be cost-effectively built to maintain temperatures above freezing and ensure filling and dewatering is possible.
Once the container is full, it will undergo a period of consolidation where dewatering continues and a composting effect reduces pathogens. Solids content can go as high as 40% and the process emits no significant odour, simplifying the handling and reuse of the solids as a soil amendment.
Replacing solar drying beds to reduce labour costs
The Meteghan Sewage Treatment Plant (STP) in the Municipality of Clare, Nova Scotia, used to spread sludge onto drying beds. Then, after drying the sludge for about a month, operators would rake it by hand into wheelbarrows and load it into trucks for disposal. It was a lengthy, time-consuming process that dramatically reduced the amount of time that operators could spend on much-needed infrastructure projects, such as plant process optimization and reducing inflow and infiltration in the collection system.
In November 2016, the Meteghan STP began using a Bishop Solids Management Solution, enabling the plant to collect and dewater the same volume of sludge in about five hours, rather than several weeks. Since commissioning, the plant has dewatered over 1 million litres of sludge and has saved hundreds of hours in labour.
Sludge from the plant is pumped directly from the sludge storage tank to a Geotube geotextile container, which provides storage, consolidation and passive dewatering of the sludge. As the sludge is pumped, a specially selected polymer is added to accelerate and enhance the dewatering process.
The dewatering cell, which occupies about 232 m2 was constructed in the same location as the drying beds and is capable of accommodating two Geotube containers. Each container is about 13.7 m in circumference and 17.4 m long.
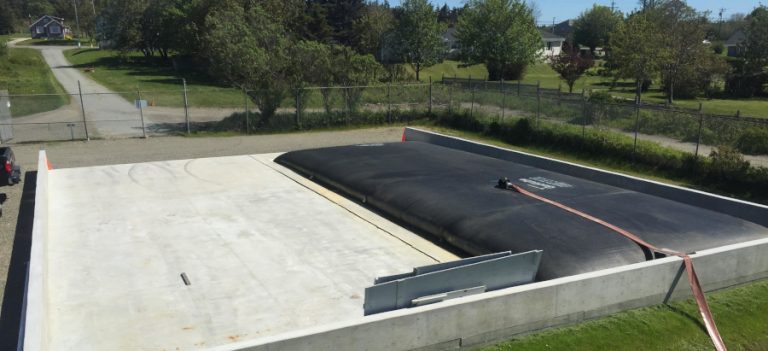
The Bishop Solids Management Solution replaced solar drying beds at the Meteghan STP to dramatically reduce the amount of time operators spend on sludge management.
A cost-effective method to accept septage at a municipal plant
The Eganville Wastewater Treatment Plant (WWTP) in Ontario, has operated a sludge and septage dewatering facility since 2008, using the Bishop Solids Management Solution. This innovative facility has a dual purpose, providing a simple, low-energy process for dewatering and stabilizing aerobically digested sludge from the municipal treatment plant, as well as septage brought in by local haulers.
The process not only simplifies sludge management from the treatment plant, it also provides a local facility where haulers can empty septage. Many treatment facilities are unable to accept septage and haulers often travel great distances to empty their trucks. This is a time-consuming process that results in added costs for property owners and increased greenhouse gas emissions from vehicles.
Sludge from the treatment plant and septage from haulers are both sent to a 37.8 m3 underground holding tank, which is recirculated once full to ensure the solids are well blended. Pumps then move the sludge to a Geotube container. As the sludge is pumped, polymer is added directly into the feed line to enhance the dewatering process and help retain contaminants in the container.
The laydown area can accommodate up to six 15.25 m long Geotube containers, two of which are set up inside a greenhouse. The greenhouse maintains an indoor temperature above freezing and enables the facility to receive and dewater sludge and septage year round.
After a period of dewatering and stabilisation, the biosolids are typically sent to the municipal landfill where they are not buried, but instead used as a soil amendment to the final cover.
Eganville WWTP continues to accept septage from local haulers on a fee-for-service model, which helps support the operation and potentially opens new revenue opportunities by extending the service to a wider area of haulers.
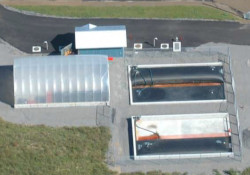
The Eganville WWTP has used the Bishop Solids Management Solution since 2008 to dewater sludge and accept septage from local haulers.