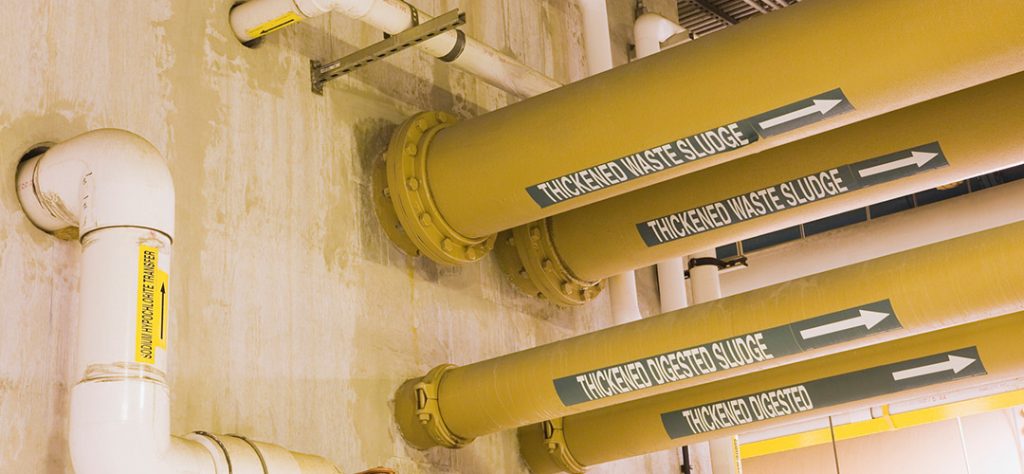
ARTICLE
Slash sludge disposal costs with ClariPhos®
ClariPhos® rare earth coagulant reduces sludge by as much as 50%
Is sludge disposal hauling away too much of your operating budget?
A 2016 report* prepared for the Vermont legislature, relying on national level EPA cost analysis, “estimated that approximately 40% of a wastewater treatment plant’s total annual operating cost is spent on solids management.” That report also predicted a future increase in solids production due to the increased need to reduce the nitrogen and phosphorus contribution from sewage into the surface water basins. This is particularly true for phosphorus (P).
Why do lower phosphorus limits increase sludge?
Unlike nitrogen, which can be effectively removed biologically, phosphorus removal is typically achieved with chemical precipitation. Traditionally, this has been done using iron- or aluminum-based coagulants. But these coagulants can produce significant amounts of sludge especially when phosphorus limits in effluent are extremely low. In some cases, phosphorus precipitation with alum or ferric coagulants can produce 12 to 16 mg/L of sludge for every mg of P removed.
Watch our video to see faster settling and lower sludge volume for ClariPhos compared to conventional Al- and Fe-based coagulants.
They operate on an adsorption mechanism, typically requiring between a 2.5-to-1 molar ratio and a 4-to-1 molar ratio of iron or aluminum to P. They also create a fluffy floc with high amounts of bound water that is difficult to separate through settling and dewatering processes. The phosphorus, a solids-dispersing agent, suspends these solids, making them more difficult to settle. The result is a sludge that remains high in water content and much more costly to transport and dispose of.
Rare earth elements (REEs) can reduce sludge by as much as 50% compared with iron or aluminum
Cerium, a rare earth element, reacts at a 1-to-1 molar ratio with P to form the mineral rhabdophane. This precipitate has a specific gravity of 4, compared with the specific gravity of iron or aluminum precipitates of between 2.4 to 3.4. Higher density solids settle better, binding less water in the process.
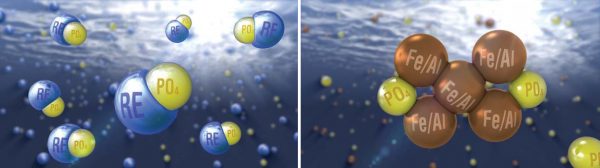
ClariPhos forms a strong, stable bond with phosphorus at a molar ration of 1:1. Fe or Al coagulants typically require at least a 5:2 molar ratio, but can go as high as 8:1 when greater P reduction is needed.
Bottom line – ClariPhos helps achieve significant sludge reduction and cost savings
One 770,000 GPD facility discharging to a tributary to Lake Erie switched to REE precipitation primarily to meet a stringent aluminum limit by removing aluminum-based coagulants. The change provided immediate compliance with the aluminum limit, but the benefits didn’t stop there. Prior to switching to REE precipitation, the plant operated a belt filter press 8 hrs/day, 5 days/week, with an average solid content of 15%. That required hauling 75, 20-yard sludge containers to a landfill annually.
After switching to REEs, the belt filter press run time was reduced to one 8-hr shift per week, at a solids content of 21%. The number of 20-yard sludge containers landfilled annually dropped from 75 to 31, resulting in a savings of $70,000 per year in sludge hauling costs alone.
AI | RE | |
---|---|---|
Belt Filter Press Operation | 40 hrs/wk | 8 hrs/wk |
% Solids | 15 | 21 |
20-yard sludge containers landfilled/yr | 75 | 31 |
Sludge hauling cost savings/yr | — | $70,000 |
Are you ready to slash your sludge disposal costs?
White Paper
Sludge Reduction Benefits Observed When using Rare Earth Technology in Wastewater Treatment
In a wastewater treatment facility, the separation of solids from water is a very important task. Typically coagulants are added in an effort to aid the process. Recently, Rare Earth (RE) technology has emerged as a new coagulant and has proven to be an effective alternative to traditional iron or aluminum based coagulants for phosphorus removal.